Membru VIP
Central electrică sticlă oțel coș de fum
Central electrică sticlă oțel coș de fum
Detaliile produsului
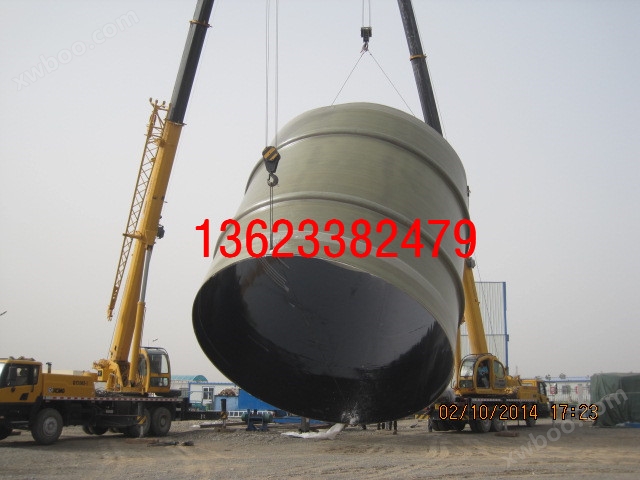

Analiza aplicațiilor coșurilor de sticlă și oțel în centralele termice
În ultimii ani, pe măsură ce cerințele naționale pentru desulfurare sunt din ce în ce mai stricte, centralele termice au adoptat cea mai mare parte desulfurarea umedă, în utilizarea metodei umede de desulfurare.Înainte de procesul de sulf, deși gazele de fum conțin mai mult dioxid de sulf, gazele de fum intră în coș de fum cu o temperatură mai ridicată, până la 130 ~ 160 ° C.
Formarea doar a unei cantități mici de expunere a gazelor de fum, cerințele de protecție împotriva coroziunii pentru coș de fum nu sunt foarte mari. Dar după desulfurare, temperatura fumului scade.
La 50-80 ° C, conținutul de umiditate al gazelor de fum este mai mare, ceea ce duce la creșterea ratei de coroziune a pereților interni ai coșului de fum. Pentru a rezolva coroziunea severă
Problema, coșul de oțel din sticlă cu rezistența sa la coroziune bună, ușoară și puternică, viață lungă, construcție ușoară, fără întreținere și alte avantaje
Aceasta oferă cea mai bună soluție și a fost promovată.
1. Caracteristicile materialelor din sticlă și oțel
Plasticul armat cu fibra de sticla (Fiberglass Reinforced Plastics) este un material din sticla.
Un amestec de înaltă performanță din combinația organică a matricului de rășină. Este compatibil cu coșuri de fum materiale tradiționale, cum ar fi beton armat, oțel, cărămidă și altele.
Comparativ cu calitatea, are următoarele avantaje:
1 Rezistență la coroziune
Oțelul de sticlă are rezistență excelentă la coroziune și poate rezista la coroziune în mai multe medii, inclusiv acizi, alcali și sare. Lista tabelului 1
În caz de rezistență la acid, coroziune de cloruri ridicate din oțel de sticlă din rășină de ester de vinil epoxid. După multe cercetări, încercări
Testarea, testarea și rezultatele au constatat că materialele din sticlă și oțel sunt cele mai bune materiale anticorozive.
2 Ușoară și puternică
Oțelul de sticlă are proprietăți fizice ușoare și puternice, proporția sa este de doar 1/4 din oțel, întinderea inelară a oțelului de sticlă înțelat mecanic
Rezistența poate ajunge la 1000Mpa, rezistența la tracțiune axială poate ajunge la 300Mpa, în timp ce rezistența la tracțiune a Q235 este de 370-500Mpa, oțel de sticlă
Este mult mai puternic decât oțelul.
3 Conductivitate termică scăzută
Performanțele de izolare a oțelului de sticlă sunt mai bune, conductivitatea termică a acestuia este mult mai mică decât conductivitatea termică a oțelului, în cazurile în care este nevoie de izolare, sticla
Echipamentele din oțel nu pot avea nevoie de straturi de izolare termică; Coeficientul de dilatare termică a oțelului de sticlă este relativ mic, mai aproape de oțel, astfel încât pentru înălțimea
Un coș de fum cu diferență de temperatură mică și scăzută nu poate avea secțiuni de expansiune. Vezi tabelul 2:
Materialul proiectului | Fibră înfășurată din oțel de sticlă | oțel | PVC |
Factor de dilatare termică (10-6/℃) | 11.2 | 12.3 | 60-80 |
Conductivitate termică (W/m ℃) | 0.23 | 41 | 0.18 |
4 Viață lungă
Viața de utilizare a oțelului de sticlă este mai lungă, în străinătate există 40 de ani de experiență în utilizarea coșului de oțel de sticlă. Conform ASTM D din SUA
Standardul 5364 prevede ca durata de viata a cilindrilor din sticla sa ajunga la 35 de ani.
5 Costuri
Dacă se ia în considerare întreaga durată de viață a structurii de inginerie, costul total al coșului de sticlă și oțel este mai competitiv decât coșul de sticlă din alte materiale, deoarece
Materialele din sticlă și oțel au avantajele de rezistență la coroziune, ușurință și putere, durată de viață lungă, costuri scăzute de întreținere și reparații, astfel încât costul lor integrat
relativ scăzută. Iată un exemplu al unui coș de fum cu o înălțime de 240 de metri și un diametru de 8 metri, pentru a face costul coșului de fum din diferite materiale
Comparație, a se vedea tabelul 3:
Tabelul 3 Comparația prețurilor pentru coșuri de fum din diferite materiale
Oțel - cărămidă de sticlă cu spumă | 18 milioane de dolari. |
Structură din oțel și titan | 21 de milioane de dolari. |
Întreg din sticlă și oțel | 15 milioane de dolari. |
2. Procesul de construcție din sticlă și oțel
În prezent, procesul de formare a coșului de sticlă și oțel este în principal automatizat pentru formarea mecanică. Avantajele modelării înveliate din oțel de sticlă: ①
Capacitatea de a se proiecta în conformitate cu condițiile de forță ale produsului, astfel încât să poată utiliza pe deplin rezistența fibrei; Mai mare decât intensitatea: în general,
Greutatea poate fi redusă cu 40-60% în comparație cu recipientele de oțel cu același volum și presiune; fiabilitate ridicată:
Produsele înțepate cu fibre sunt ușor de realizat mecanizarea și automatizarea producției, după ce condițiile de proces sunt determinate, calitatea produselor înțepate este stabilă și precisă;
4. eficiență ridicată de producție: utilizarea de mecanizare sau de producție automatizată, necesită mai puțini muncitori de operare, viteza de înlăturare rapidă (240 m / min), astfel încât
productivitatea ridicată a muncii; Costuri reduse: pe același produs, mai multe materiale pot fi alese în mod rezonabil (inclusiv rășină, fibre și căptușire),
Îi recompilezi pentru a obține cele mai bune rezultate tehnice și economice. Toate coșurile de sticlă și oțel fabricate acum sunt înțepate cu automatizare controlată de calculator.
Aplicația oțelului din sticlă în centralele termice
3.1, aplicarea coșului de sticlă și oțel din străinătate
Aplicarea de coșuri de sticlă și oțel din străinătate a început în anii 1970, încă din 1977, în Statele Unite ale Americii EastKentucky
Power Cooperative a folosit cu succes un coș de sticlă și oțel la centrala electrică Spurlock
Diametrul de 15,5 ft, 4,73 m) este încă în siguranță. În perioada 2004-2008, numărul de coșuri de sticlă și oțel construite în Statele Unite,
După cum se arată în tabelul 4. Câteva cazuri tipice de utilizare a coșului de fum în fiecare țară sunt prezentate în tabelul 5.
Tabelul 4Numărul de coșuri de sticlă și oțel construite în America de Nord în ultimii ani [4]
anii | 2004 | 2005 | 2006 | 2007 | 2008 |
Doș de sticlă și oțel Numărul construit |
33 | 35 | 38 | 49 | 53 |
Tabelul 5Utilizarea construcțiilor de coșuri de fum FRP în străinătate
Locație | Observaţii | Anul |
Stația de energie Spurlock din East Kentucky Power Cooperative | Diametrul coșului de fum 4.73m Înălțimea 245 | În 1977. |
Centrala electrică Santee Cooper |
Diametrul coșului de fum 8.54m Înălțime 148.8m | În 2004 |
Centrala electrică Kraftwerk Simmering | Diametrul coșului de fum 8.54m Înălțime 148.8m | În 2001 |
Centrala electrică Ingolstadt | Diametrul coșului de fum 6.7m Înălțime 180m | anul 1993 |
Centrala electrică din Kansai, Japonia | Diametrul cilindrului interior de 5,3 m, lungimea tubului de 11 m, 51 de tuburi din sticlă și oțel asamblate | anul 1992 |
Centrala electrică Eggborough | 2 unități de 500 MW cu două cilindri interioare FRP de 184 m | anul 2002 |
Centrala electrică Neideraussen, Germania | Unități 1000MW | anul 2003 |
Centrala experimentală Voiklingen, Germania | Unitate de 300 MW | anul 1982 |
Centrala electrică Schwaree Pumpe | Unitate de 2 x 800MW | anul 1997 |
Centrala electrică Weisweiler, Germania | Unitate de 2300MW | |
Centrala electrică din Lippendorf, Germania | 2 x 920 MW unități | |
Centrala electrică Vresova | Unitate de 125 MW | anul 2000 |
În 2007, centrala electrică P4, care a fost remodelată în SUA, a construit un nou coș de fum cu două cilindri, proiectat de PullmanPower.
Cilindrul exterior este din beton armat, înălțime 131.064m, diametru 20.599m, cilindrul interior este din FRP, diametru 8.1m, rășină
Se utilizează rășină HetronFR992. Învârșirea și instalarea în câmp a cilindrului intern, fiecare cilindru intern este împărțit în 12 segmente, fiecare 9,144 m.
În 2002, centrala electrică Eggborough din Marea Britanie a adăugat unități F GD umede pentru două unități de 500 MW.
În același timp, două cilindri din FRP de 184 m au fost instalate în coșul de beton.
În iulie 2000, centrala cehă Vresova de 125 MW a semnat un contract pentru adăugarea sistemului F GD umed, cu coșuri de oțel
Structura susținută de coș de fum FRP.
Centrala electrică Kraftwerk Simmering, construită în Germania în septembrie 2001, cu o înălţime de 200 m şi un diametru de 4,8 m
Coș de fum FRP. În plus, Germania a fost, de asemenea, primul în lume care a adoptat tehnologia de unificare a cigatoarelor, folosind FRP pentru a fabrica rânduri cu diametru de 7-10 m.
Conduce de fum.
În Japonia, unitatea de 800 MW a centralei electrice Nangang din Kansai Electric utilizează un coș de fum cu 3 cilindri interiori FRP, diametrul cilindrului interior FRP
5.3 m, Înălţime 200 m.
Adesea în străinătate de ani de cercetare și aplicații de inginerie, s-a format partea de proiectare, fabricare și construcție a structurilor de coșuri de fum sau conducte FRP
Standarde de suprafață, cum ar fi ASTM D 5364 din SUA.
3.2, aplicația coșului de sticlă și oțel intern
China în ceea ce privește cercetarea și aplicarea coșurilor de sticlă și oțel în spatele țărilor dezvoltate occidentale, dar în ultimii ani, coșurile de sticlă și oțel, cum ar fi după ploaie
Proiectele finalizate în prezent includ centrala electrică Hutu Wall din Xinjiang, centrala electrică Anhui Huai North Tiger Mountain, centrala termică Panjin Liaodong Bay și altele, sunt în curs de pregătire.
Construcția include centrala electrică Chongqing Shizhu, Taiyuan II Thermal, Shandong Binzhou și alte centrale electrice.
Majorele institute de proiectare a energiei electrice și institutele de proiectare a energiei electrice provinciale au utilizat în prezent coșul de sticlă și oțel ca opțiune principală de proiectare.
Compania noastră este o unitate de redactare participantă la standardul național GB30811-2014 >> Standard pentru cilindrul intern de coș de sticlă îmbunătățit cu fibra de sticlă pentru centralele electrice de cărbune.
4. Comparația dintre cilindrul interior al coșului de sticlă și oțel și placa de titan
Titanul este un material cu o rezistență excelentă la coroziune, datorită faptului că suprafața titanului generează ușor o membrană de pasivare stabilă și, prin urmare, în acid
Soluția de sare alcalină, alcalină și neutră are o stabilitate mai bună, dar schema de plăci de titan are următoarele dezavantaje:
(1) Plăcile de titan sunt costisitoare și sunt cele mai scumpe din toate schemele.
(2) ciclul de fabricație a plăcii de titan este, de asemenea, cel mai lung, de la comandă la livrare durează cel puțin 3-4 luni, chiar și jumătate
Mai mult de un an.
(3) Tratarea sudurii plăcii de titan este o problemă foarte complexă, tehnica de sudură a plăcii de titan în sine este foarte dificilă, nu
Sudorii obișnuiți pot fi construiți, trebuie să treacă prin instruire tehnică specializată, în același timp, deoarece multe construcții sunt efectuate în aer înalt, sudura
Dificultatea de conectare este mare, astfel încât multe probleme de calitate a coșurilor de titan apar în principal în apropierea sudurilor.
(4) Deoarece aliajul de titan și coeficientul de dilatare al plăcii de oțel sunt diferite, sunt ușor de produs fisuri.
5. Comentarii și sugestii
Cu o rezistență mai bună la coroziune, ușoară și puternică, ușor de instalat și utilizat în comparație cu cilindrul interior din oțel și sticlă
Viața lungă, facilitățile de întreținere și alte avantaje, cu perspective mari de piață.
Odată cu introducerea standardelor naționale relevante, cum ar fi GB50051 "Specificația de proiectare a coșului de fum" "GB30811-2014>> Proiectarea și fabricarea coșului de oțel și sticlă în standardul de cilindru interior al coșului de fum îmbunătățit cu fibra de sticlă
Cu dispoziții clare, acest lucru va stimula, de asemenea, o aplicație mai largă a coșului de sticlă și oțel în industria electrică.
Cerere online